Understanding Porosity in Welding: Checking Out Reasons, Results, and Avoidance Methods
Porosity in welding is a persistent challenge that can dramatically affect the quality and honesty of welds. As specialists in the welding market are well aware, comprehending the causes, impacts, and avoidance techniques connected to porosity is important for accomplishing robust and trusted welds. By diving right into the origin creates of porosity, examining its harmful results on weld quality, and checking out reliable prevention methods, welders can improve their knowledge and skills to create premium welds consistently. The intricate interplay of elements adding to porosity needs a detailed understanding and a proactive method to make sure successful welding end results.
Usual Root Causes Of Porosity
Contamination, in the form of dirt, oil, or corrosion on the welding surface area, develops gas pockets when warmed, leading to porosity in the weld. Inappropriate securing happens when the securing gas, generally utilized in procedures like MIG and TIG welding, is unable to completely protect the liquified weld swimming pool from reacting with the surrounding air, resulting in gas entrapment and subsequent porosity. Additionally, insufficient gas coverage, often due to incorrect flow prices or nozzle positioning, can leave parts of the weld unguarded, allowing porosity to create.
Results on Weld Top Quality
The visibility of porosity in a weld can substantially compromise the overall top quality and honesty of the bonded joint. Porosity within a weld creates gaps or cavities that deteriorate the framework, making it a lot more at risk to breaking, deterioration, and mechanical failure.
Moreover, porosity can impede the effectiveness of non-destructive screening (NDT) techniques, making it challenging to find various other flaws or stoppages within the weld. This can result in considerable security issues, especially in essential applications where the architectural integrity of the welded elements is extremely important.
Avoidance Techniques Summary
Provided the damaging effect of porosity on weld top quality, efficient avoidance methods are vital to maintaining the structural stability of bonded joints. Furthermore, choosing the ideal welding criteria, such as voltage, current, and travel speed, can aid reduce the risk of porosity formation. By incorporating these avoidance techniques right next page into welding methods, the incident of porosity can be substantially decreased, leading to stronger and extra reputable welded joints.
Significance of Proper Shielding
Correct shielding in welding plays a vital role in protecting against climatic contamination and ensuring the stability of welded joints. Shielding gases, such as argon, helium, or a combination of both, are typically utilized to shield the weld pool from reacting with components airborne like oxygen and nitrogen. When these reactive components enter contact with the warm weld pool, they can cause porosity, bring about weak welds with minimized mechanical properties.

Poor shielding can lead to various flaws like porosity, spatter, and oxidation, compromising the architectural honesty of the bonded joint. Sticking to proper protecting techniques is crucial to create top notch welds with click for source minimal problems and make sure the durability and dependability of the welded parts.
Surveillance and Control Approaches
Just how can welders successfully keep an eye on and manage the welding procedure to ensure optimal results and stop issues like porosity? One key approach is with making use of innovative surveillance modern technologies. These can include real-time monitoring systems that offer feedback on specifications such as voltage, present, travel speed, and gas circulation prices. By continuously keeping an eye on these variables, welders can recognize inconsistencies from the excellent problems and make prompt modifications to prevent porosity development.

Furthermore, implementing appropriate training programs for welders is important for keeping track of and regulating the welding process successfully. What is Porosity. Educating welders on the importance of keeping regular specifications, such as appropriate gas securing and travel rate, can aid avoid porosity issues. Normal evaluations and qualifications can additionally ensure that welders excel in monitoring and regulating welding processes
In addition, making use of automated welding systems can enhance surveillance and control abilities. These systems can exactly manage welding criteria, lowering the likelihood of human mistake and guaranteeing consistent weld view quality. By combining innovative tracking innovations, training programs, and automated systems, welders can properly check and regulate the welding process to decrease porosity issues and attain top notch welds.
Verdict
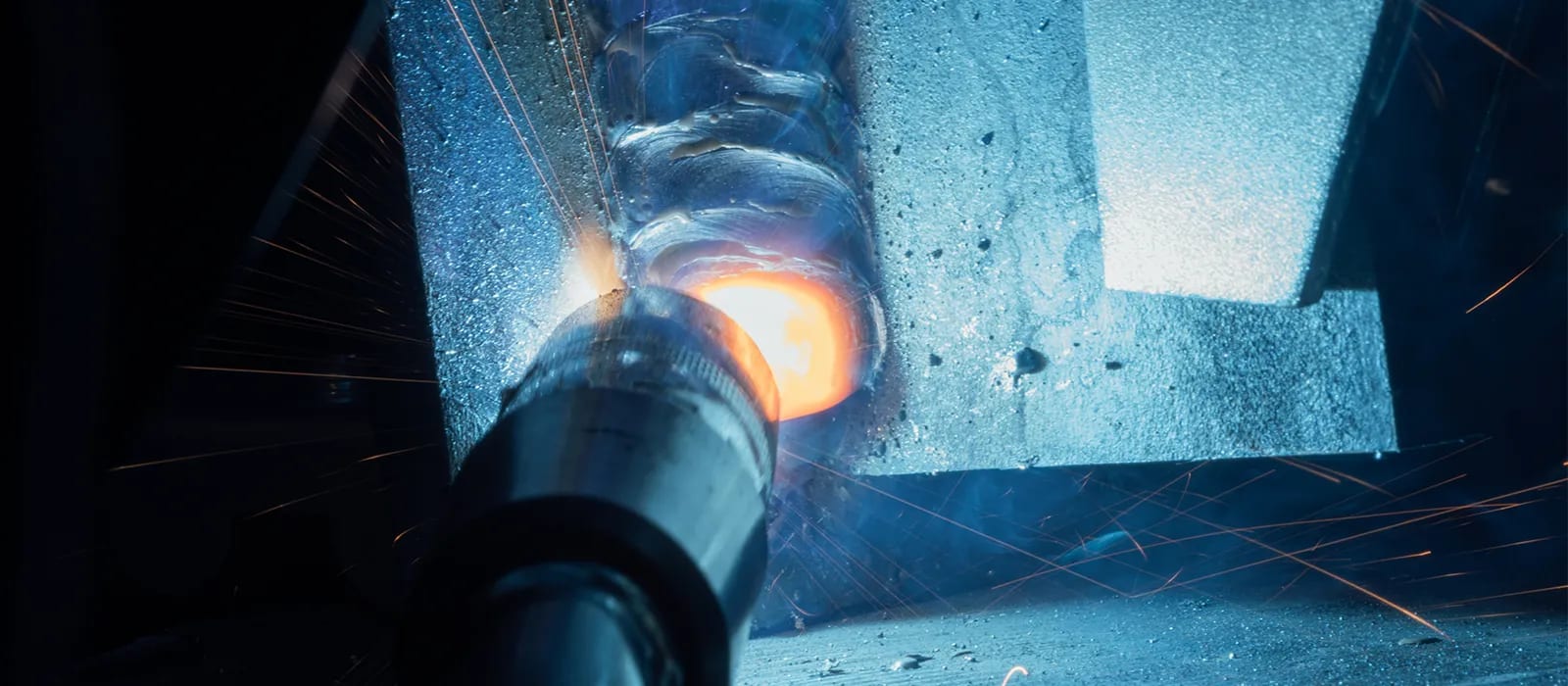